The TMA group has specialised in metal cutting for over 40 years and continues to invest every year in the latest generations of cutting machines. Particularly suited to series cutting, plasma cutting has now been added to range of services offered by the Group, allowing it to meet the full range of customer needs.
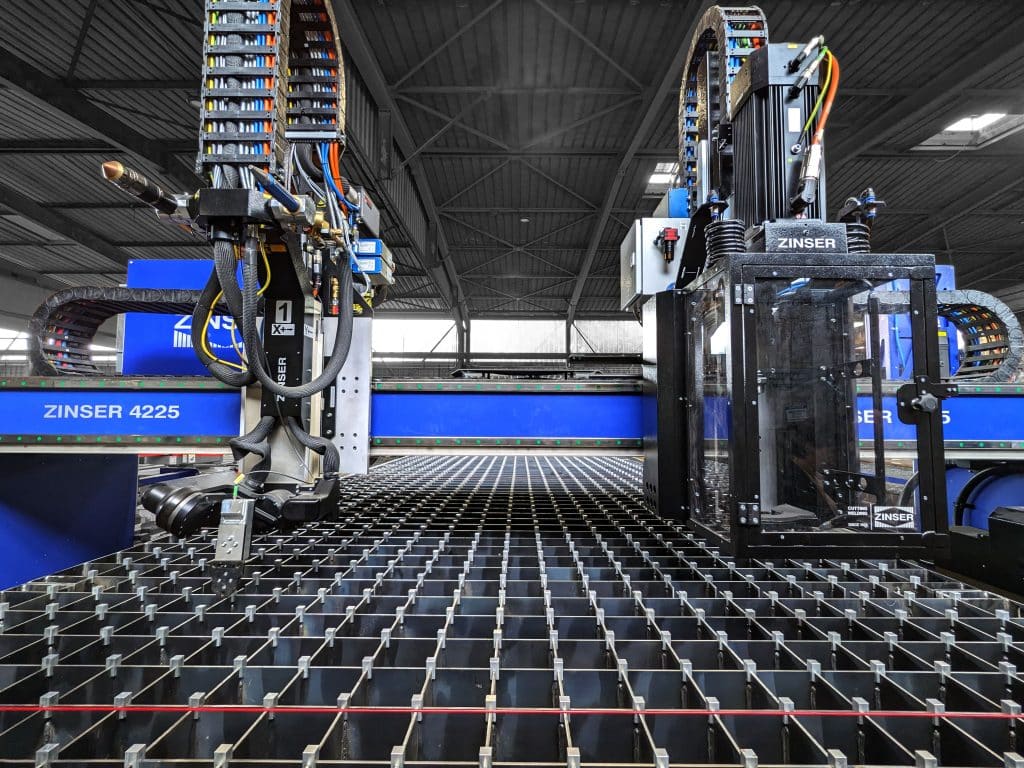
Ideal for cutting medium or thick metal plate
Plasma cutting, a method widely used in the metallurgical industry, relies on the generation of an electric arc. This process ionises gases to create a hot plasma that melts on and cuts through the metal.
TMA Group’s plasma cutter can cut steel, aluminium and stainless steel plate from 6 to 50 mm thick on a 3000 x 17000 mm cutting bed. This versatile plasma machine has two cutting heads and offers multiple capabilities.
Plasma cutting with additional services
With numerous options available, the high precision plasma cutting machine easily adapts to meet the needs of all your projects. In addition to the plasma cutting process, this machine also offers other processing capabilities such as drilling, tapping, countersinking and marking as well as top and bottom straight-edge and circular bevel cutting.
Plasma cutting is particularly suited to medium and thick materials, especially ferrous and non-ferrous metals. Steel, aluminium, stainless steel and copper are all compatible with the plasma cutter. Checker and embossed plate can also be cut.
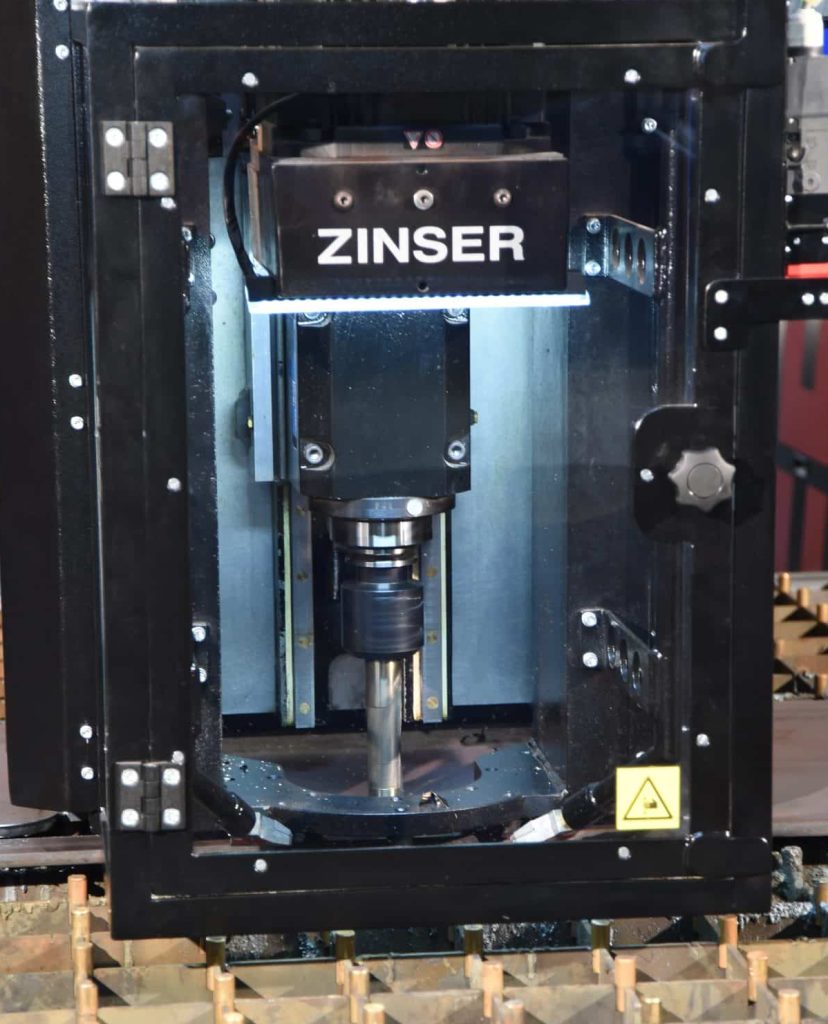
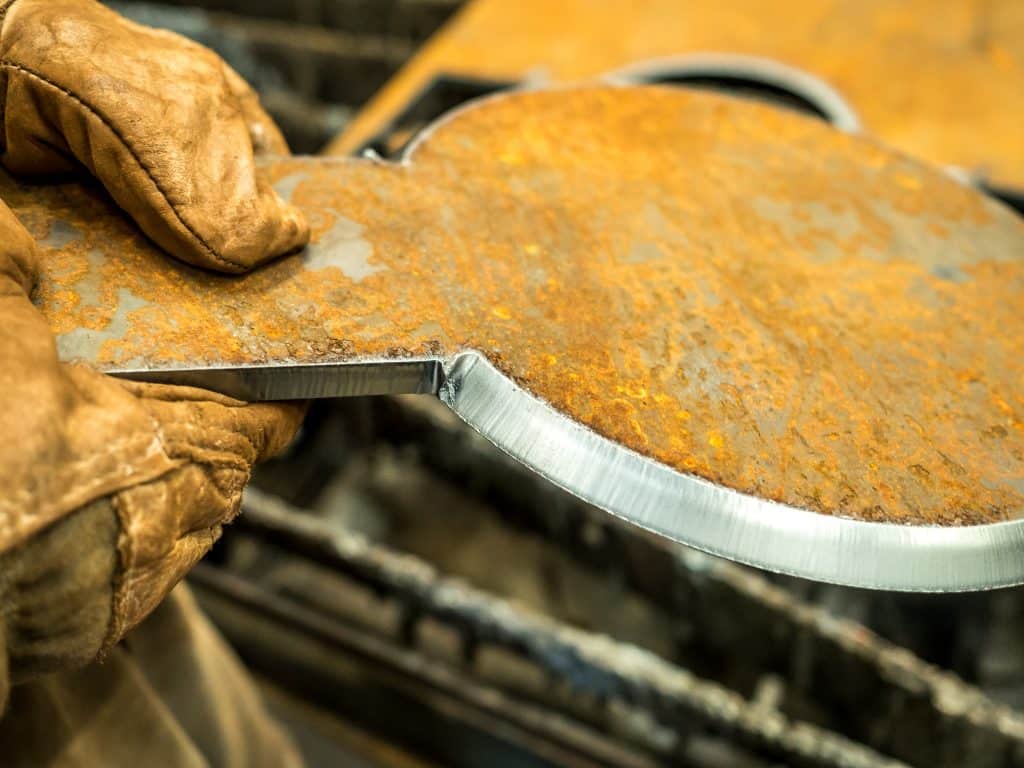
What is the difference between plasma, flame and laser cutting?
Plasma cutting occupies a position somewhere between flame (oxy-fuel) cutting and laser cutting. Unlike flame cutting, which uses oxygen to burn the metal, plasma cutting produces more precise, cleaner cuts, with less deformation, thanks to faster cutting which reduces the HAZ (heat-affected zone) on the part. Compared to laser cutting, plasma can cut thicker parts.
The plasma machine has the advantage of offering extra options on top of the plasma cutting function. Its drilling unit, with its automatic tool change magazine, is able to perform different machining operations. Drilling, tapping, countersinking, milling and bevel cutting can all be done directly on the plasma machine, reducing handling and saving time in the manufacturing of metal parts.