Specialising in waterjet cutting, the TMA Group makes custom parts for industrial customers in short or long production runs. Waterjet cutting lends itself to a very wide range of materials: steel, aluminium, stainless steel, rubber, stone, wood, glass and many others. All our services are performed in France by cutting experts with only one aim in mind: customer satisfaction.
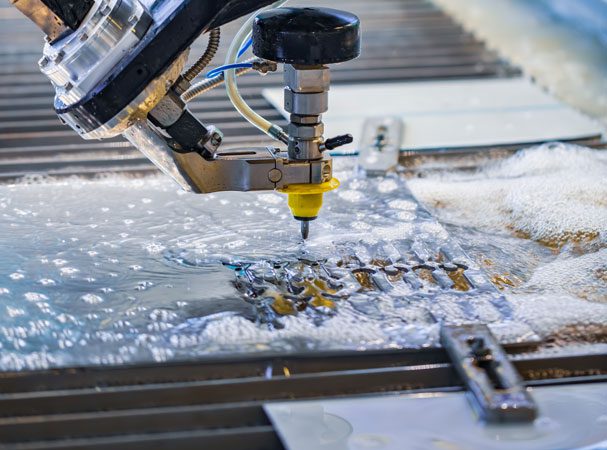
How does waterjet cutting work?
This technology is a cold cutting process that uses the force of water at high pressure to remove and separate material. Using a high pressure pump that can reach 6000 bar, the machine propels the water through a fine nozzle to generate a powerful hair-thin stream of water. As it exits the cutting head the waterjet hits the surface of the material to begin a cutting process that does not generate heat and therefore does produce heat affected zones.
Waterjet cutting is extremely versatile and can be used on any type of material. However, depending on the material and how thick it is, the water may be pure or have an abrasive added. Pure water is used to cut softer materials such as foam, rubber, plastic and even fabrics, while water mixed with abrasive particles is capable of cutting harder materials: metals, composites, stone, glass, etc.
Why use waterjet cutting in industry?
As in laser cutting, waterjet cutting machines are CNC operated. The difference lies in the degree of precision, which is higher than that of laser cutting machines. Waterjet cutting is able to meet the needs of industries with the most demanding tolerances.
In particular we work with companies in the nuclear, defence and precision engineering sectors.
Waterjet cutting is also an interesting alternative to oxy-cutting for very thick parts. Although cutting times can be longer, this technology does not produce heat affected zones, thereby protecting the material from distortion. Depending on the type of part and its end use, in some cases it is indispensable to opt for a mechanical cutting process rather than a thermal process.
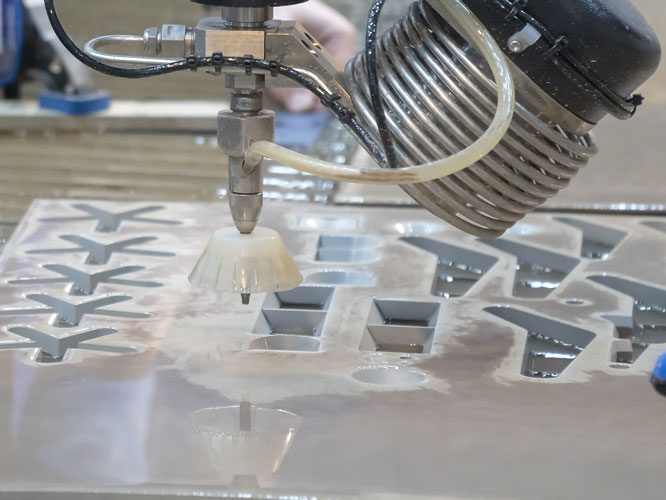
Benefits of waterjet cutting
Our waterjet cutting service for steel, stainless steel, aluminium and any other material
The TMA Group is equipped with a waterjet cutting machine capable of 2D and bevel cutting. Its 6200 bar high pressure pump creates a jet powerful enough to cut through thicknesses of over 150 mm for certain materials. We can cut any type of material on a table sized 2000 x 6000 mm.
Waterjet cutting for more environmentally friendly manufacturing
More precise than a laser, this technology produces the narrowest of kerfs, limiting material loss and optimising part nesting. Underneath the cutting table there is a catcher which absorbs the high pressure of the jet and collects the water used in the operation. This container is then emptied and the water recycled. Unlike machining and other, thermal cutting processes, waterjet cutting produces no chips, burrs or gas emissions.
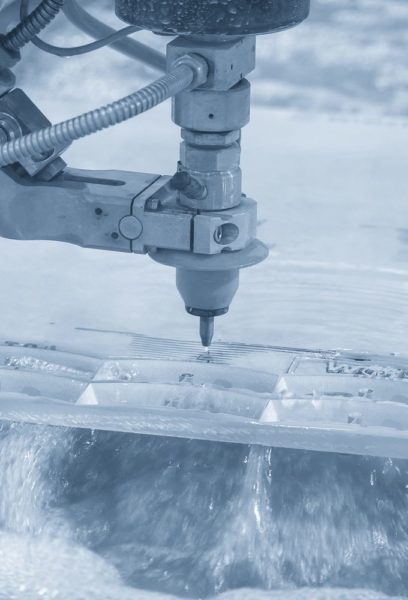
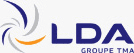
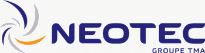
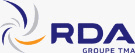
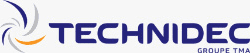
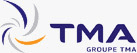